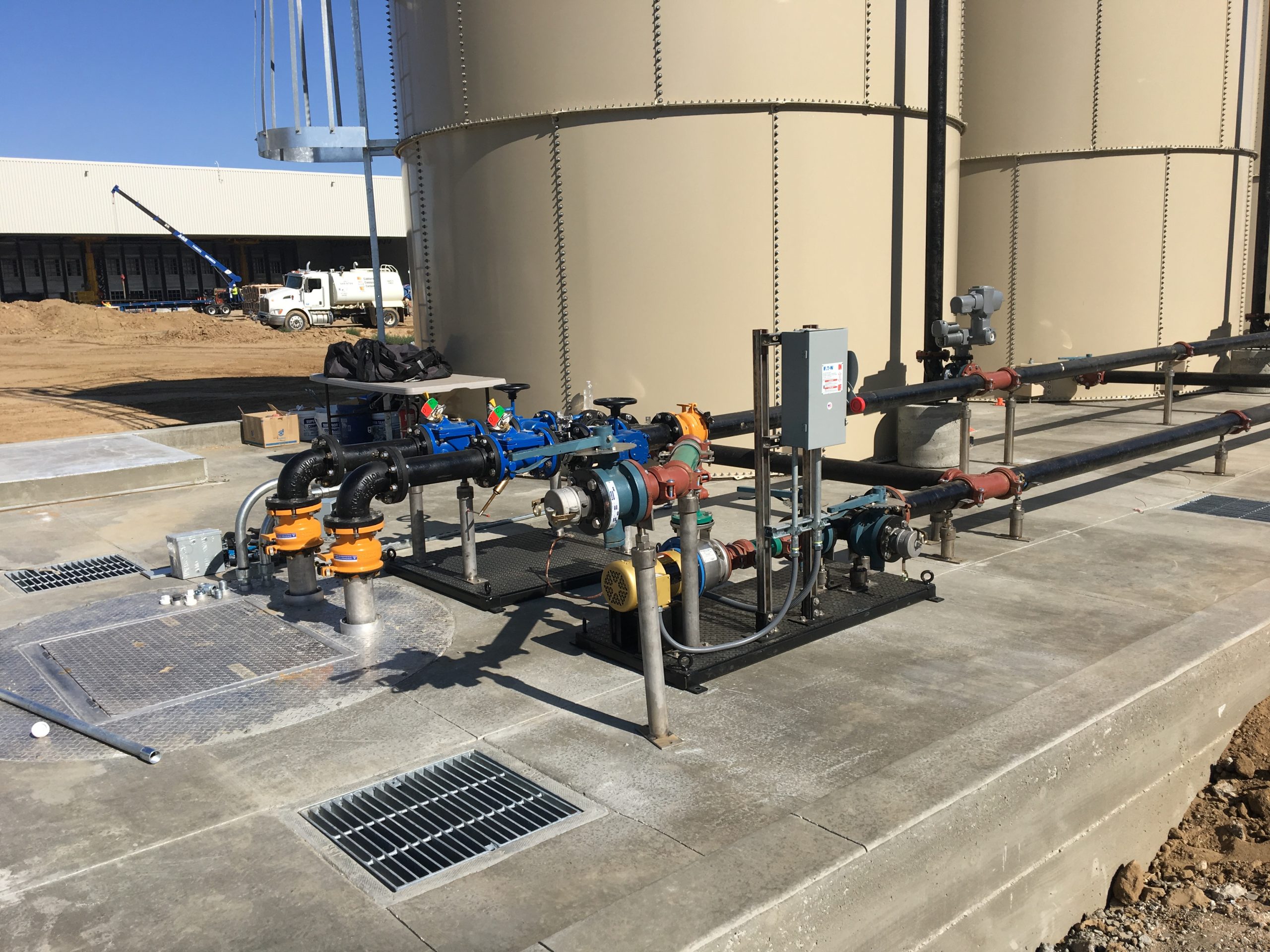
At Romtec Utilities we work with owners, developers, and engineers on pump station designs to deliver the system they need for their project.
For our pump station projects, our customers typically choose to use the traditional “bid” procurement method to try and save money. But this bid method can take time and money away from the finished product.
There is another, more effective public purchasing method that meets most legal requirements in order to procure a pump station for your project.
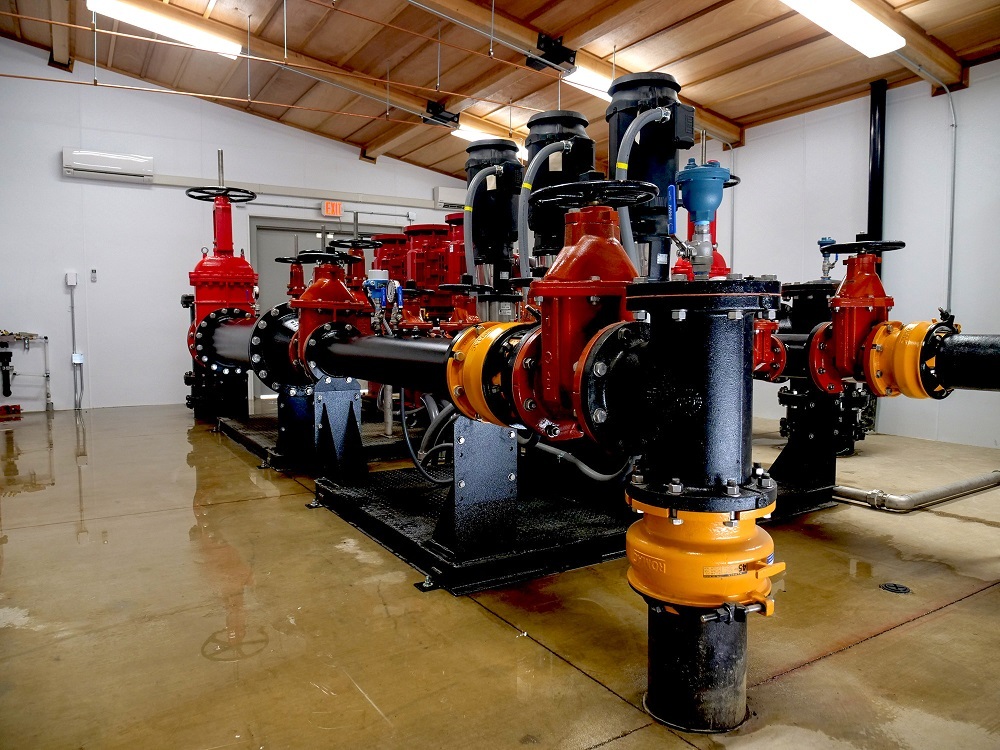
The Design-Build Method
Design-Build ensures that the awarded entity is capable of all aspects of the project while eliminating bidders without experience or capability which ultimately reduces the risk for the end owner.
A design-build specification means that owners only receive bids from companies that can do both the design and building of the project. It puts the focus on experience and qualifications, not just the lowest bid, which doesn’t always provide the best value.
The design-build method cuts out the need for additional bidding processes which take time and money. The owner drafts an initial project requirement and asks for proposals from design-builders who give their best price along with notes on the requirements. This process drives collaboration between the owner and the design-build company which reduces change orders and streamlines the entire process.
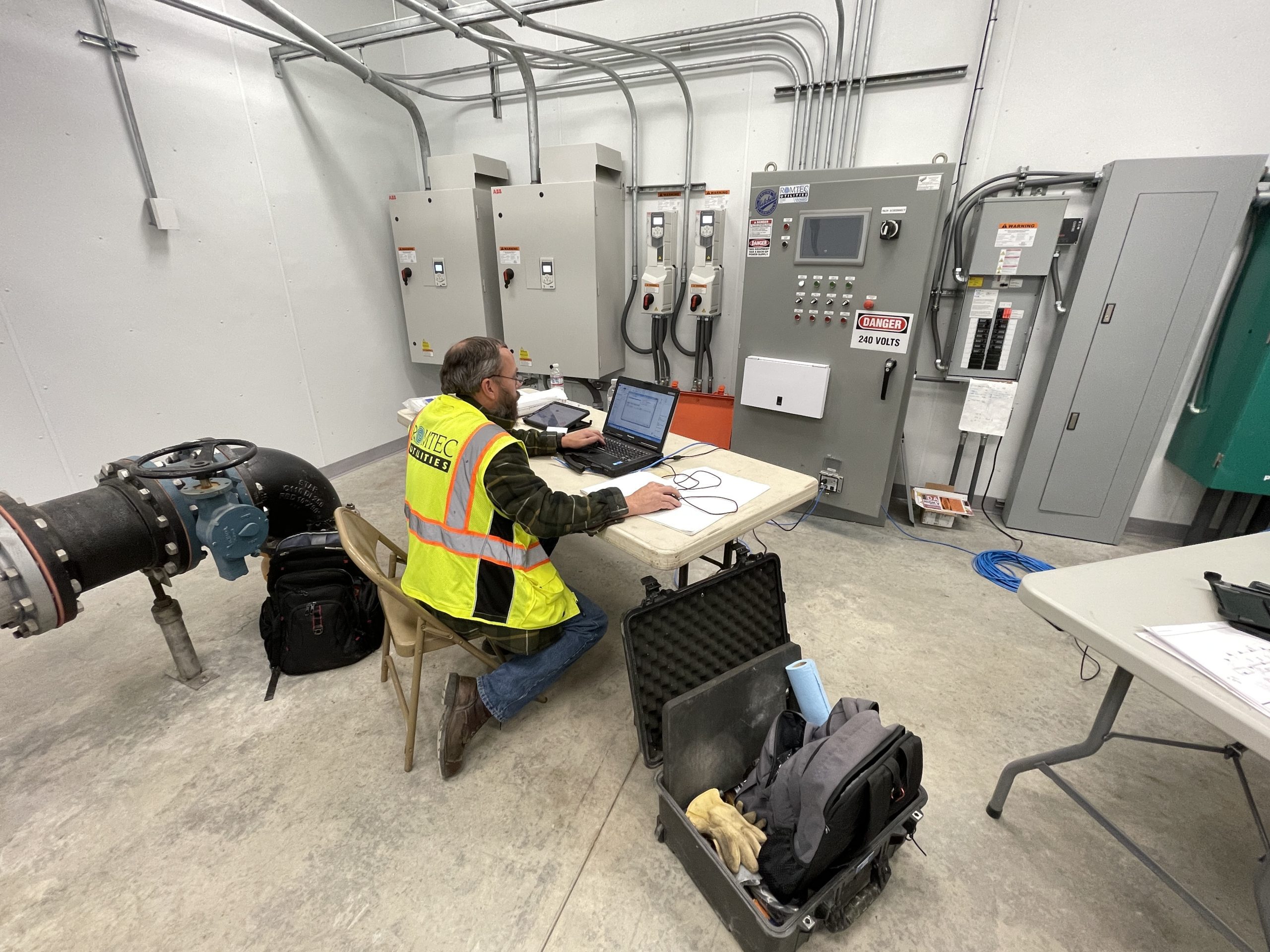
Detractors of the Traditional Bid Method
The traditional bid process slows down the project as it takes time to put a project out to bid twice (first for design and second for construction), receive all the bids, and go over them all. Bid packages are expensive and managing the bid process for both design and then for construction is extensive on staff (resources).
The best price at the end of the bid process does not mean the best value if both the contractor or supplier isn’t qualified or experienced for the project.
Incompetent designs or contractors, change orders and unsatisfied owners are common with the traditional bid process.
The traditional bid methodology has engineers or architects designing without a thought of availability. In the current environment of scarcity in construction materials, this leads to projects being bid with expensive and unfeasible designs due to incorporating materials that are or are not available.
Overall, the price, time, and collaboration level (or lack of) between engineers and the general contractor, or the installing contractor, can all take away from the finished product.

Benefits of The Design-Build Method
The Design-Build approach is growing in popularity with public and private entities for various reasons.
First, there little to no lower initial investment in plan development prior to the bid.
Design flexibility and material flexibility provide a greater level of maneuverability to change parts or configurations which is important in the current supply chain environment.
This approach reduces time as projects are awarded and completed faster and cleaner because there is more collaboration in the design-build method between the owner and the hired design-builder. It also reduces finger-pointing and drives real collaboration within a defined budget.
Romtec Utilities Design-Build
At Romtec Utilities we have completed various design-build projects for our pump systems with a high level of success for our customers.
Ultimately, they receive the best value and best quality when choosing Romtec as we have the experience and capability to design, manufacture, supply, and install our pumping systems all over the country with this method. Saving time, money and gaining value for the end owner.
The old design-bid-build process has fallen short of creating the best value for the project and end owner. But the Design-Build method has created a new avenue for owners, developers, and engineers to get the best value with a high level of collaboration and design flexibility.
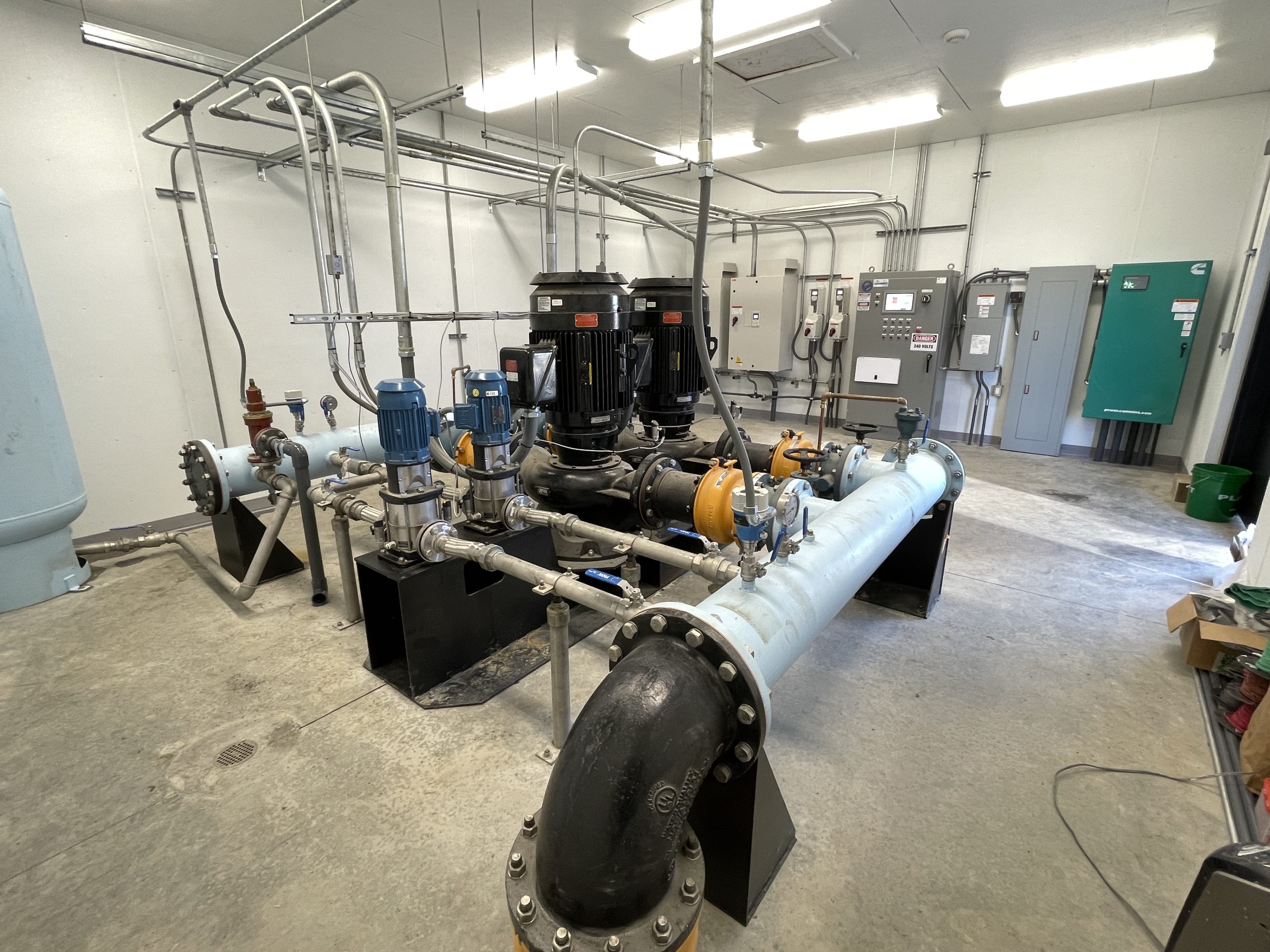
Design Build vs. Traditional Bid Project
The design-build process starts off with collaboration between Romtec Utilities, the project driver, and the end owner deciding what they want to build or need to build in regards to a lift station as part of a larger project.
Instead of bidding out the design portion of the project to an architect or engineer, the owner hires a single company to create the engineered drawings, supply the materials, and build the project.
The owners write a specification and go through a vetting process to determine which companies qualify to do the design-build project based on their experience and expertise. Once they determine who has the experience to complete the design-build, they put out an RFP (Request for Proposal).
The RFP goes into detail about the proposal of services (design, materials procurement, demolition, construction, etc.) that will be covered under the design-build contract agreement between the two entities if they win the project. The proposed schedule and the pricing proposal is also included in the RFP.
Then the owner reviews all the proposals and eventually selects the company they feel is the best fit for their project.
Design work then begins in a collaborative manner between the owner and the company. Once the design is approved, then the construction plans can be sent for review by the local authority. A high level of collaboration happens in this process between the design and construction disciplines to ensure designs are feasible from a construction and supply standpoint.
Construction of the project commences with the design-builder as the responsible party for the completion of all aspects.
Best of all “Design Build” represents a real alternative to the old two-part bid process which first requires a bid to ultimately award a contract to an Architect/Engineer and then a second bid and contract to award the project to a contractor for construction. With “Design Build” we now have a proven, legally acceptable, alternative method to consolidate the full responsibility of all aspects of any project into a single bid that allows bidders to present their credentials as well as their price proposals. Design Build then awards based on the overall scope, quality, completeness, and experience of the various design build bidders as opposed to just price.
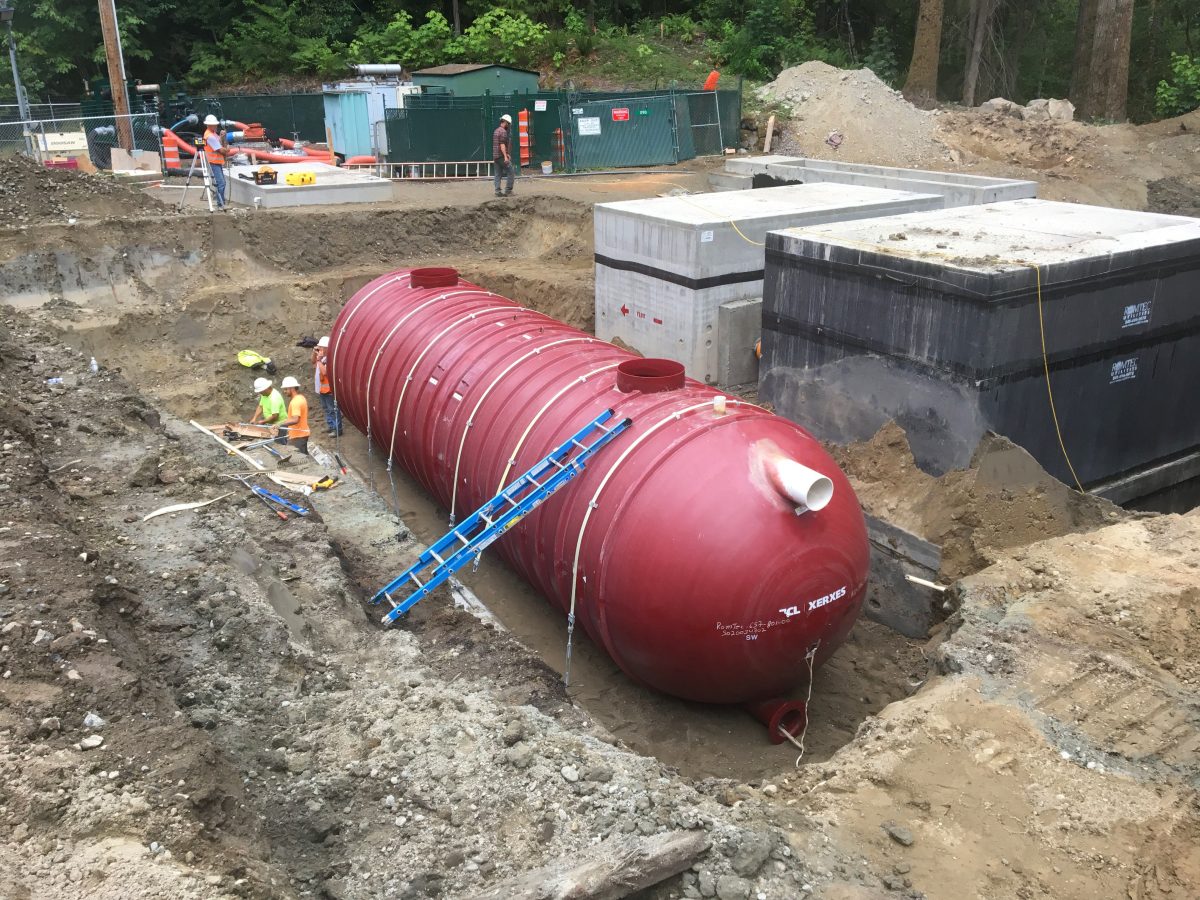
Design/Build is a real breakthrough. It has been used for large projects for years. Now, it’s a very practical solution for projects that are smaller, but just as important.
The lack of collaboration between the two entities (designer/builder) in the traditional bid process can lead to projects failing, not getting done, or going way over budget and schedule. This is due to the designer and builder not working together to accomplish the same goal for the owner. This is completely avoidable with the “Design-Build” procurement method.