Glycol Recovery Systems
Pumping Systems to Handle Glycol Pumping & Recovery
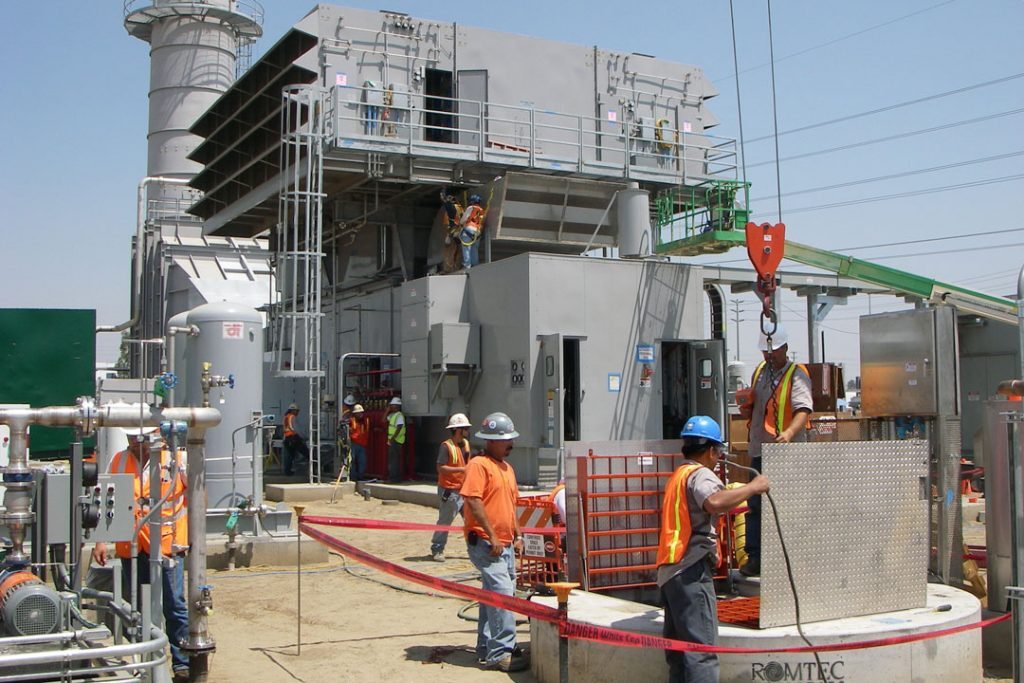
We Can Meet Your Required Lead Times for Glycol Pumping
Romtec Utilities will help your project move fast by working through your lead times for a glycol recovery system. Our production process will prefabricate major components like skids and vault assemblies so that your system is ready for installation at the time of delivery.
We Work with Any & All Brands for Lift Station Components
For pumps, control panels, flow meters, or any other components, Romtec Utilities will engineer and supply your pumping system with your preferred component brands. Our engineers research and work with component manufacturers worldwide and offer a wealth of experience utilizing or recommending any and all component brands.
We Provide Expert Engineering Documents for Your System Approval
Our engineered drawings include complete documentation that clearly list the full scope of system components with data sheets and specifications. It also includes the full scope of services provided by Romtec Utilities to help integrate your glycol recovery pumping system into a larger project or existing site.
We Provide Modern Pumping System Telemetry & Monitoring
Romtec Utilities provides many types of remote monitoring and system telemetry for glycol recovery systems. Depending on your preferences and system operations, Romtec Utilities offers telemetry configurations that range from simple alarms and lights to robust two-way communications for more demanding sites.
Getting a Glycol Recovery Systems Station

Engineering
Romtec Utilities provides full engineering and design services to meet the specific goals of your project. Romtec Utilities’ Engineers are experts in water conveyance systems across a wide array of water types and applications. We work with our clients through every step of the process, from preliminary designs and budgetary estimates, submittal and review processes, installation, and all the way through start-up, training, and warranty.

Project Support
With Romtec Utilities you gain the support of our dedicated project management team at every step-from planning through installation. Romtec Utilities covers a vast scope of services that help execute the design, supply, construction, testing, and training of your pump system to ensure its success at the site location.

Manufacturing
Romtec Utilities provides a high level of system prefabrication prior to delivery of the system to the jobsite. This greatly reduces construction cost and installation time, as well as potential project delays and change orders. This high level of prefabrication can often reduce installation time from weeks to days. Additionally, Romtec Utilities takes pride in our quality control processes, ensuring that when the system is delivered to the job site everything will function as designed.

Construction
Romtec Utilities ensures the quality and success of every pumping system from the early stages of design, all the way through installation and construction. Romtec Utilities will send experienced installation advisors to the site who will advise the installing contractor throughout the installation process providing all parties with the reassurance that the station is constructed and ultimately functioning as designed.

Commissioning
Romtec Utilities’ startup, testing, and training services are essential to the success of any pumping system. Following installation our technicians are on-site working directly with all parties to field check the control panel, operate the pumps, perform system testing, and provide world class training to all maintenance personnel.

Warranty
With Romtec Utilities, every complete pump station is covered with a standard one-year warranty. Romtec Utilities also provides ongoing support from our entire team throughout the lifetime of our products. This support is provided to ensure that every pump and lift station project is successful.