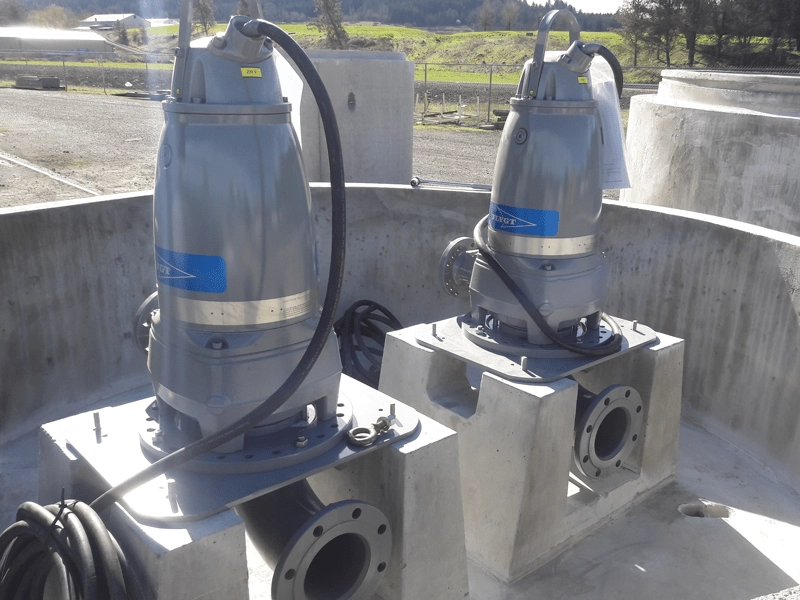
Pumps are vital components in every pump station that Romtec Utilities designs, engineers, and manufactures, and our systems make use of all types of pumps for all applications. One prominent difference in pump designs is the way the motor is cooled. Pump cooling systems prevent overheating by transferring heat from the motor to outside the pump. There are several types of cooling systems commonly used in pumps. These are direct contact, integrated cooling, internal cooling, and external cooling. The most efficient cooling system can vary between applications depending on water type, pump location, and pump starts per hour.
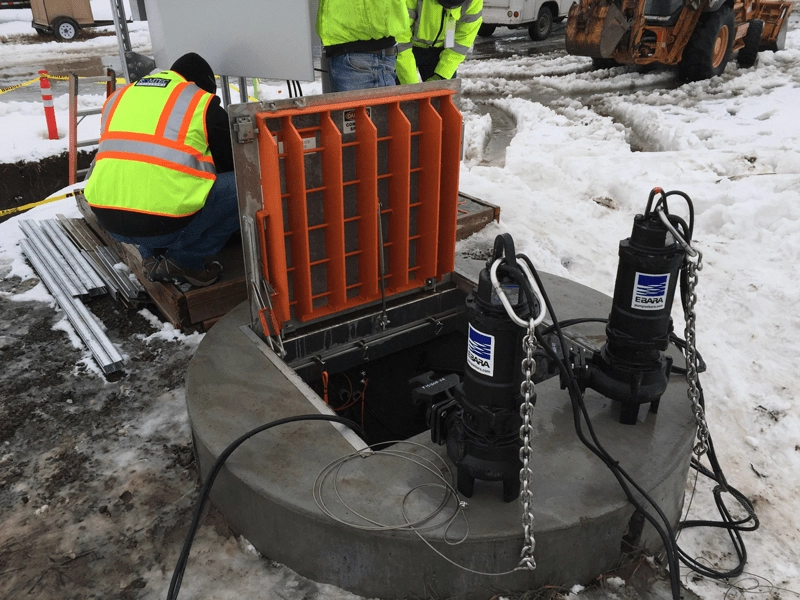
Overheating is a leading causes of pump failure in pumping systems. High-quality pumps often include thermal sensors to protect against overheating. These sensors detect when a motor reaches critical temperatures to prevent continuing damage. The right cooling system will transfer excess heat from the motor and disperse it to prevent heat from building up. With direct contact cooling systems, the pumps operate while submerged in the liquid being pumped. Romtec Utilities utilizes submersible pumps in many of our pumping systems, especially wastewater and stormwater. This cooling system is passive and requires time. A deeper active pumping range will reduce the number of starts per hour, allowing more heat to disperse between cycles. Direct contact is suitable in applications with relatively low temperatures in the well.
Integrated cooling is another cooling system used in pumps. While operating, a small flow of the pumped liquid is circulated between the pump’s cooling jacket and stator housing. This cooling system uses forced conveyance to transfer excess heat from the motor to the pumped liquid as it flows through. Unlike direct contact, the pump does not need to be submerged in the wet well or sump and can operate outside of the well. This cooling system can introduce foreign particles inside the pump housing. Typically, pump manufactures will prescribe a minimum velocity for the flow inside the cooling jacket to prevent any build-up. Cooling jackets allow a much more efficient transfer of heat to take place inside the pump, but integrated cooling also relies on applications with relatively low temperature fluids.
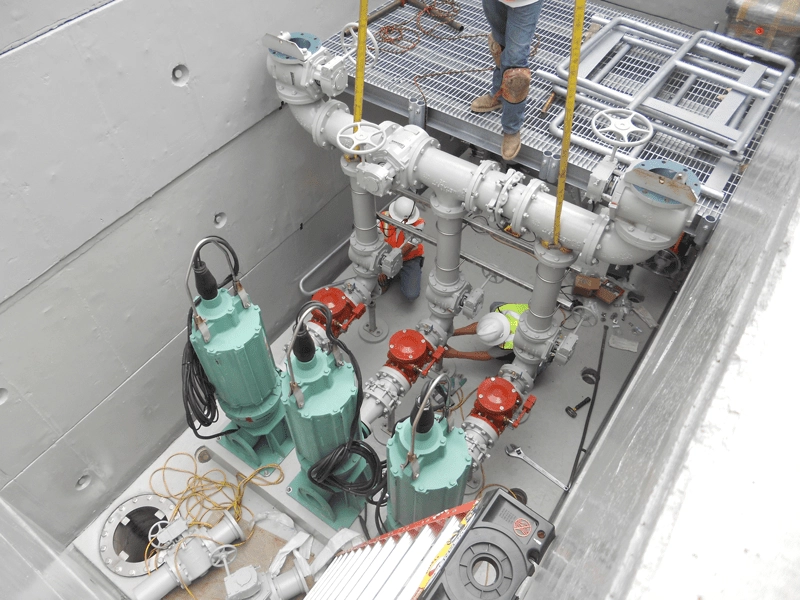
Internal cooling is similar to integrated cooling. The only difference is the fluid that is circulated in the cooling jacket. Internal cooling systems use oil or another cooling medium to regulate the temperature of the pump motors. These systems are very effective and can be used in many different applications, like industrial settings with hot water. Maintenance on pumps with internal cooling is much less frequent as there are no foreign particles introduced to the system. One other cooling system shares these same properties but add greater efficiency.
External cooling systems also use a cooling jacket to regulate temperature. However, unlike internal cooling, the cooling fluid is often water supplied from an external source. The heat transfer in these systems is much more efficient because of the lack of recirculation within the pump. External cooling is often used in super-hot liquid applications or systems with heavy duty pumps that need extra cooling. Some external cooling systems will even mix the cooling water with glycol for better heat transfer. Unlike other cooling systems, the flow of cooling water is handled independent from the operation of the pump.
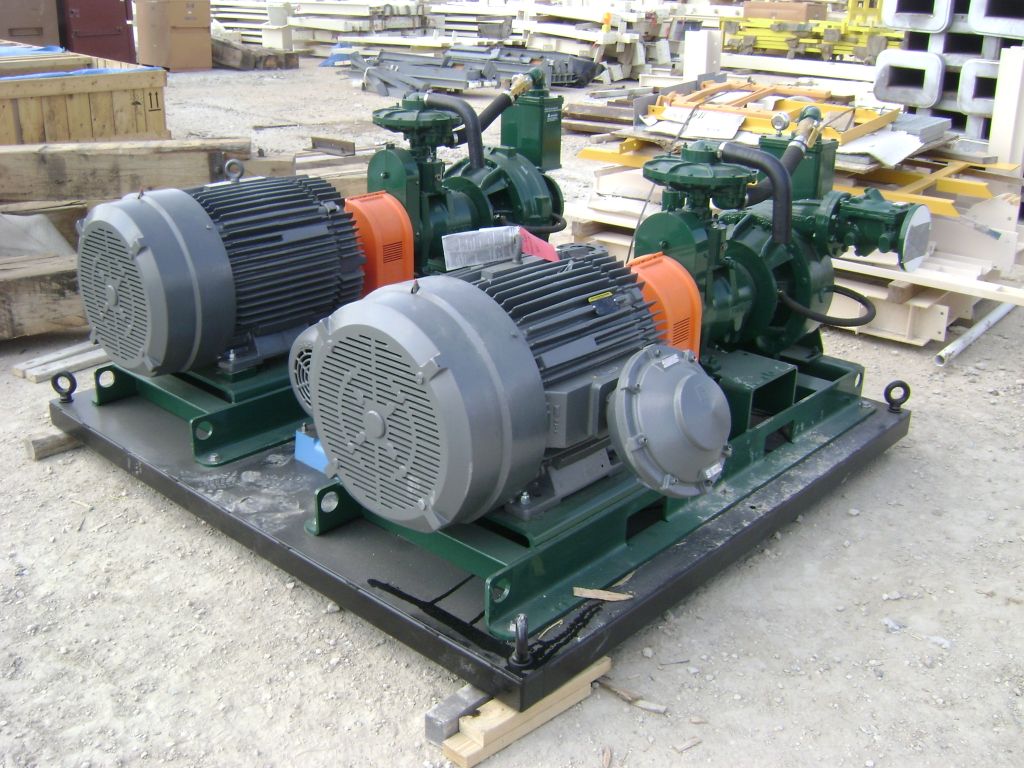
Romtec Utilities has engineered pump stations to include all types of cooling systems for the pumps. In addition to these systems, other engineering techniques can impact overheating pump motors, such as the pump station active volume, maximum pump starts per hour, and redundant pump cycling. Partnering with an experienced package pump station designer like Romtec Utilities gives you access to expertise specific to all types of pumping systems in all types of unique applications. Call our Sales Team today for more information on what pump is the best fit for your project.
Comments 2
This article provides valuable insights into the significance of cooling systems for pump motors. It effectively outlines the various cooling techniques and their importance in maintaining optimal performance and longevity of the motors. A well-structured and informative read for professionals in the field.
This article provides a good overview of pump cooling systems. Direct contact is ideal for low-temperature wells and offers passive cooling, while integrated cooling is more efficient for transferring heat but requires proper flow rate to avoid clogging.