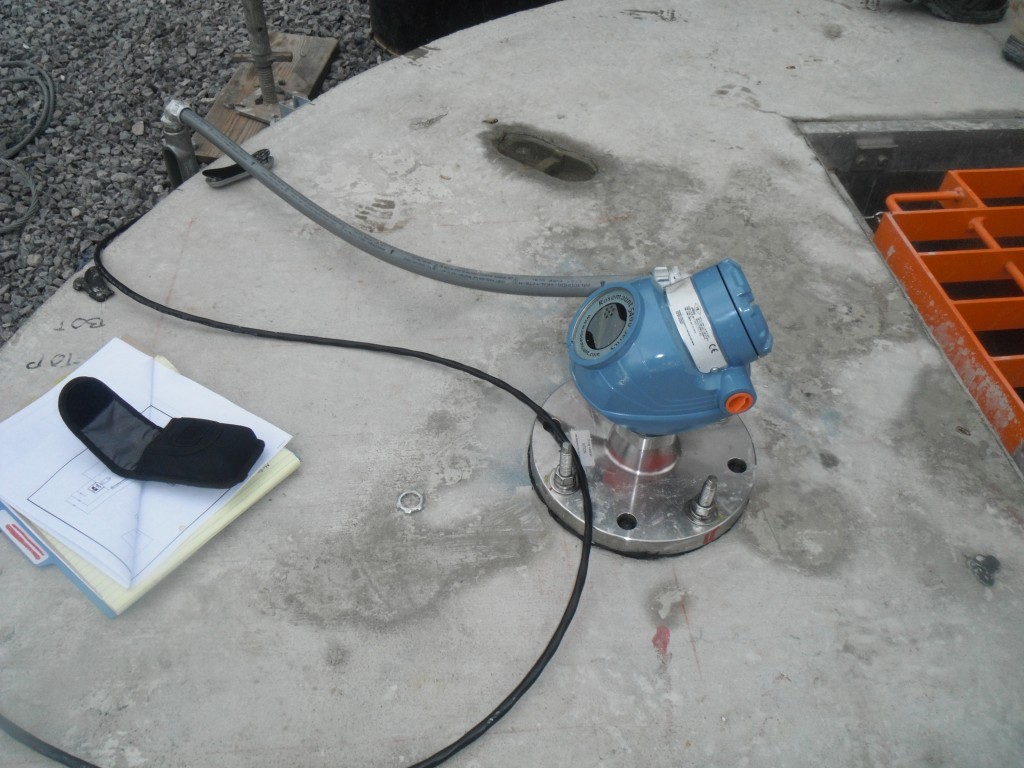
Romtec Utilities can include a lot of design options in a packaged pump station. Level sensing can be one of the most vital components during pump station engineering, and many operators and engineers have passionate opinions about which option works the best. Romtec Utilities designs its packaged pump stations to meet the needs and expectations of its owners and operators no matter which method they prefer. Each method of level sensing offers distinct advantages, and Romtec Utilities is happy to recommend a level sensing device that will benefit your unique system.
Floats
There are a few basic types of floats. Mechanical floats actuate a switch that is triggered as the float tips from vertical to horizontal. Magnetic floats operate similarly. A magnet on the float pushes a magnet on the switch mechanism with the same polarity. As the float tips horizontal, the polarity pushes the switch to complete an “on” circuit. The “off” circuit is completed as the switch and float return vertical. Mercury floats use mercury to complete a circuit. Mercury flows between to contacts as the float tips allowing an electric signal to pass to the lift stations controls. Environmental regulations in many states do not allow mercury floats.
Floats are almost always the lowest costs solution for level sensing. They are easy to adjust and replace, and additionally, floats can be visually inspected for maintenance purposes. Floats can either be counter weighted to the specific gravity of effluent or tethered to a substrate. The use of floats is limited because they must be submerged in the liquid being measured, meaning corrosive, abrasive, incongruent, or overly-viscous liquids can create maintenance or operation problems.
Probes
Like floats, conductive probes are suspended into the wet well and make contact with the effluent. Probes utilize a series of contact points that transmit a small current as the effluent fills the wet well. The lift station controls initiate a response as each set of contact points is triggered. Even though probes utilize an electrical current that makes contact with the effluent, they can operate with an intrinsically safe barrier. Intrinsically safe barriers allow the probe to operate with such small electrical currents that the liquids and gasses in the wet well are in no danger of combusting.
Probes cost more than floats by provide a durable solution. Probes are not typically affected by turbulence or grease and debris build up. Probes are typically easy to install and maintain because they can be visually inspected for build-ups. In clean water or food processing pumping applications, probes contain no harmful elements such as mercury that could possibly contaminate a system, making probes environmentally friendly.
Pressure Transducers
Pressure transducers operate on a basic mathematic assumption. If you know the liquid that is being collected and you know the size of your wet well, you can easily figure out the pressure at each depth mark in the well. The pressure transducer uses a diaphragm to measure the pressure of the liquid in the wet well and assumes its corresponding depth. The pressure transducer can in this way relay information to the lift station controls to execute the appropriate actions.
Pressure Transducers are extremely accurate and can be adjusted to keen detail. Pressure transducers also require computation to function, so this means of level sensing is an excellent choice for adding redundant lift station controls. Pressure Transducers are also very robust units that typically don’t require a lot of maintenance.
Ultrasonic Transducers
With proper maintenance, the ultrasonic transducer is a reliable and robust level sensing devise. Ultrasonic sensors do not make contact with effluent, making wear and tear a small concern. Ultrasonic sensors work by sending out high-frequency sound waves that create, in effect, an echo off the surface of the liquid in the wet well. The sensor then measures the time gap between sending the signal and receiving its echo. This time gap is directly proportional to the distance from the sensor to the level of the liquid in the wet well.
This sensor can be extremely accurate, but it does require proper maintenance. The device itself is pretty failsafe, but foam, cobwebs, dust/mist, and other impediments can affect the normal functions of the device. To a large extent, these concerns can be eliminated by selecting Ultrasonic sensors for specific water types, but as long as operators are aware of the issues, these devices perform well for extended periods of time. Ultrasonic transducers do require a clear field of view to the water surface, so the lift station engineering must understand the viewing range of the device and keep that space clear of hardware.
Bubblers
Bubbler systems have been in use for a long time, and some operators swear by them while others consider them outdated. An air compressor outside of the wet well pumps air through a “dip tube” that goes to the bottom of the wet well. This first part is true of all bubbler systems, and the air issuing from the dip tube is where the name bubbler is derived. As the wet well fills, the compressor must pump more air to maintain the bubble stream. Another air tube stems off from the dip tube and can hook up to several different devices. One device that was mentioned above is the pressure transducer. In this scenario, the transducer measures the air pressure increase as the wet well fills. Another measuring device uses the air pressure to push mercury up a tube like a thermometer. As mercury rises with the air pressure, it touches contact points that complete relay circuits.
Bubbler systems are a simple technology that is time-tested and has been proven to work under many conditions. The dip tube needs to be checked for build up and potential blockages that could misrepresent the pressure in the wet well. These systems are typically used in wastewater applications and can have accuracy issues in other water media such as slurry and corrosive liquids. Some bubbler systems will experience high installation costs because most of the system is located outside of the wet well and needs a separate storage structure.
Radar
Radar sensors operate in a similar way to the ultrasonic transducers. The difference is that radar devices utilize radio waves instead of sound waves to create an echo or in this case a wave reflection. Radar devices have the broadest range of use with different water types, and they are not generally affected by changing viscosities, pH, pressure, temperature, density, etc. Radar devices do not require heavy maintenance, and can even be programmed to ignore objects in their field of view. This means that the lift station engineering does not have to provide a 100% clear field of view for this device, making simplified configurations possible.
Radar is typically one of the most expensive devices at installation; however, the lifetime operation and maintenance costs are lower and can repay the investment with time. These devices are extremely smart. They do not require recalibration often and can utilize their operating systems for primary or redundant lift station controls.
Within each category of level sensing device, there are many models and options in order to provide a device specific to the water type and design of each packaged pump station. There are many considerations when selecting a level sensing device, and Romtec Utilities is happy to recommend an appropriate device for your system. Romtec Utilities also understands that experience and comfort level with a device is extremely important. We will always honor a customer’s request for a preferred device and design a functional and cost effective packaged pump station with their preferences in-tact. Please contact the Romtec Utilities sales staff with any questions you might have on level sensing devices or any other query about lift station engineering.