
In this Part 3 of this blog series, we will take a look at another form of level sensor that operates outside of the well. Last week, we looked at ultrasonic transducers, a reliable form of level sensing that utilizes sound waves to detect elevation changes and calculate volume. Ultrasonic transducer function reliably in scenarios where it is not suitable to have the level sensor submerged in the well or where the operations personnel prefer to access the device outside of the well. We also discussed that ultrasonic transducers include drawbacks, such as misreading resulting from turbulence, foams, and dust or cobwebs. This is where radar really excels.
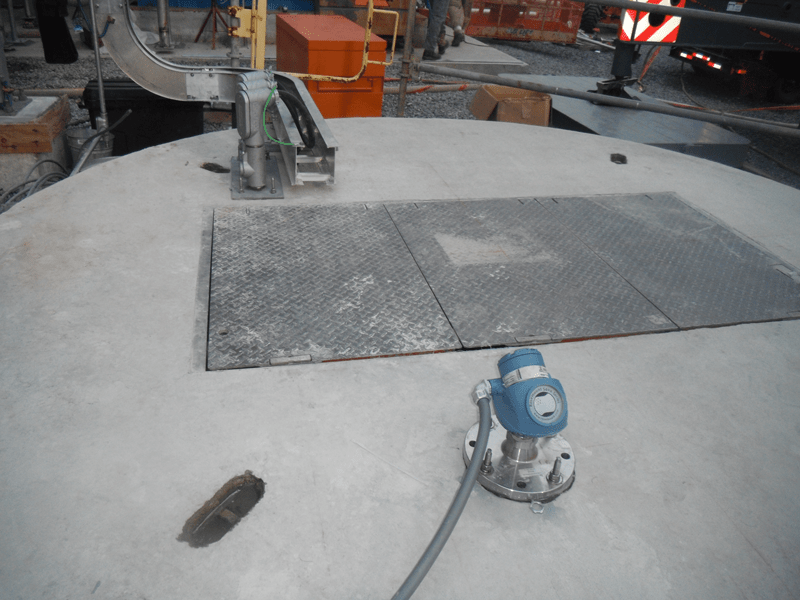
Radar uses a different burst to detect changing liquid levels. Instead of sound, radar uses electromagnetic waves to bounce signals off the surface of the liquid in the well. These waves travel faster than sound waves and can also react differently to different surface densities. This allows the radar to be programmed to ignore certain surfaces for sensing. These can include fixed surfaces like discharge piping or mounting hardware, or these surfaces can include foam, steam, and other in-well conditions that can be problematic for ultrasonic transducers. Radar is the highest cost form of level sensing but it is extremely reliable and can be configured to account for many different variables, making a very robust option.
Orlando Utilities Commission – Super-Hot Water Pump Stations
The Orlando Utilities Commission, OUC, needed a new pump station at a natural gas power plant for its combined cycle, HRSG system. This industrial process water gets super-heated during the combined cycle process and arrives in the well very hot and creates steam. These conditions make in-well sensors impractical due to the hazardous operating conditions from the heat. The presence of steam consistently make ultrasonic transducers a problematic sensor as well. For OUC, the best level-sensing device available for this pumping scenario was a radar. Mounted to the surface, a radar can “ignore” the steamy conditions and operate outside of the very hot water conditions.
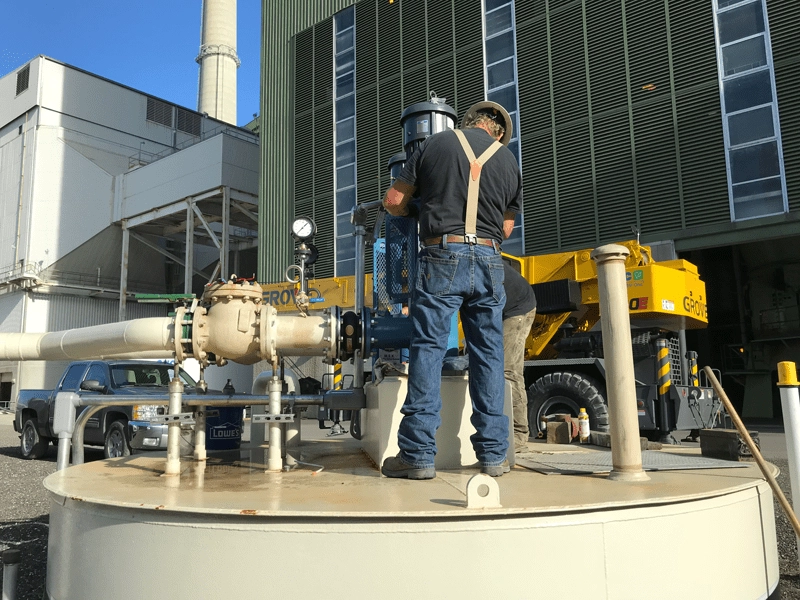
Praxair Hydrogen Refinery – Mixed Water Pumping Conditions
A new Praxair refinery in St. Charles, Louisiana needed a pump station to handle water from multiple sources, including blowdown from cleaning process and stormwater from the facility. From both sources, this water had the potential to be varying temperatures and to include varying viscosities. The cleaning process would potentially carry hydrocarbons in various forms from the process to develop “clean” diesel. The stormwater also had the potential to develop into oily water from site machinery and other conditions. Radar was an ideal choice as it could be programmed to specifically recognize liquids that were known to be present in the water and at the facility. This was the best way to provide a long-term level sensor to accommodate any current or future water conditions and pump the water reliably to onsite treatment
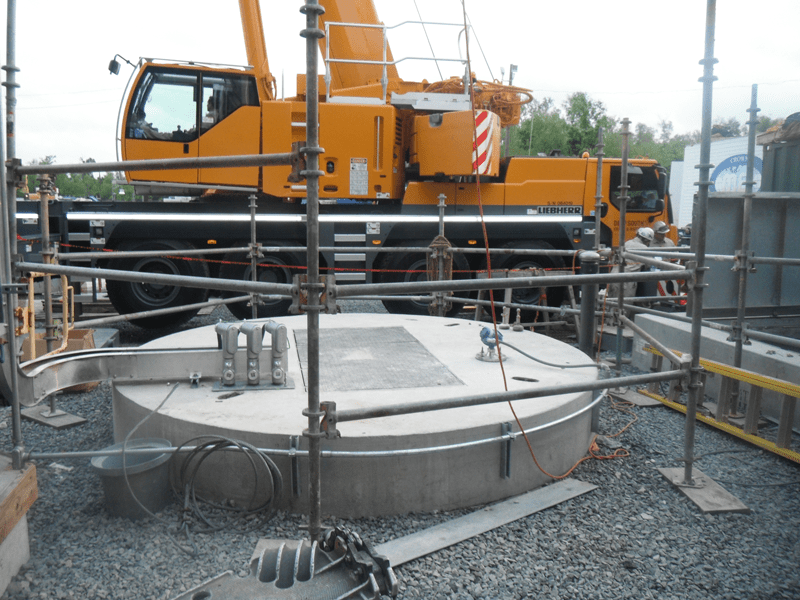
Radar level sensors do have a high cost, but they are extremely versatile. In many industrial locations, radar is the standard level sensing technology because of all the advantages that it offers. Additionally as a surface-mounted technology, radar is great for maintenance personnel in private applications. Next week we will take a look at pressure transducers as one of our most commonly supplied level sensors for many different applications!