Fiber-Reinforced Modified Polyamine Epoxy Coating
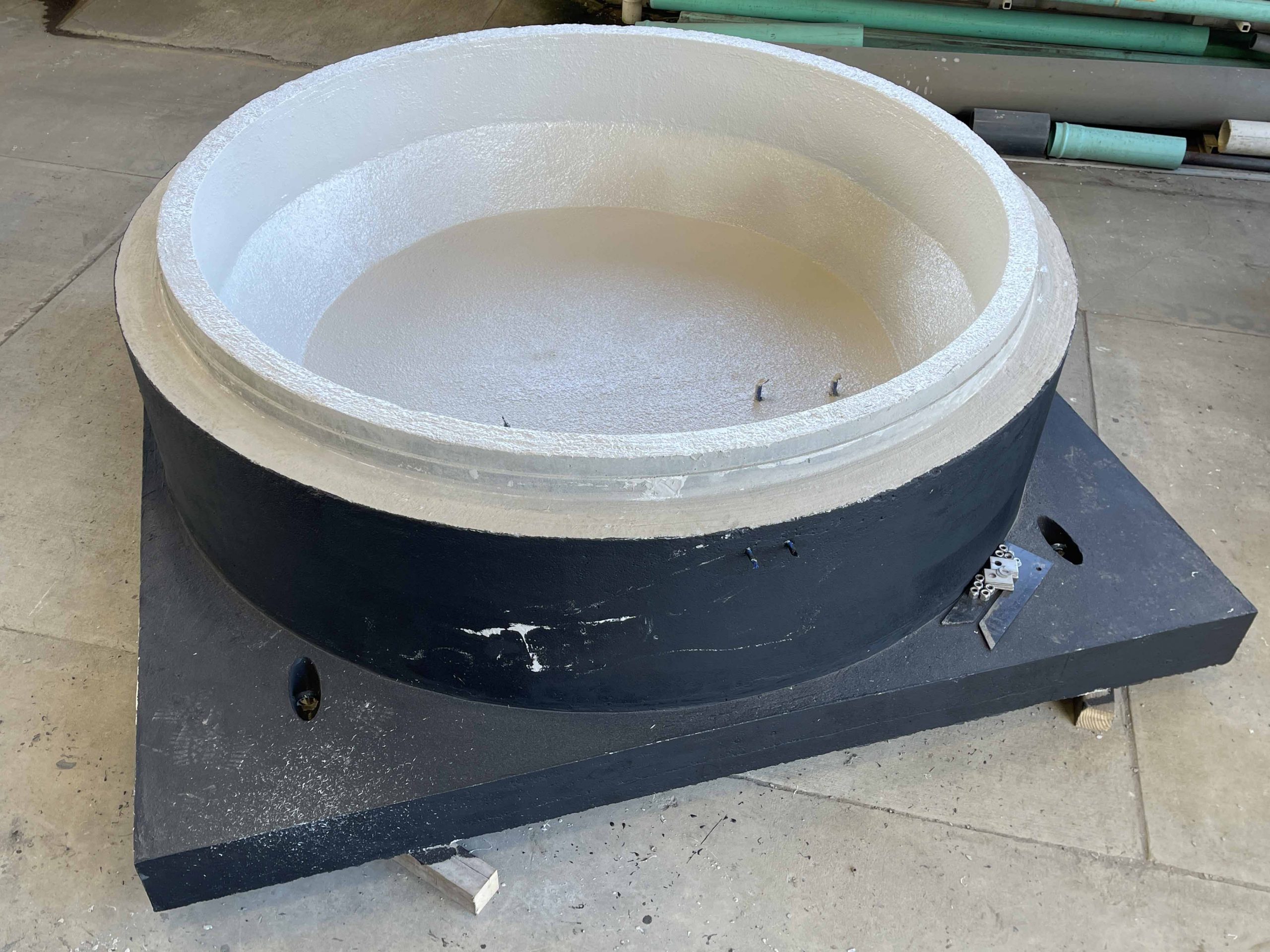
Romtec Utilities is always expanding our offering to suit our customer’s needs and is looking to solve the problems that have burdened lift stations for years. Lift stations can contain corrosive and dangerous chemicals that damage wet wells and reduce the life of the lift station. In recent years, coatings have gained popularity for lengthening the life of a system while benefitting from the lower cost of concrete wet wells. To give the best to our customers, Romtec Utilities now offers Tnemec Perma-Shield coatings that can be applied at our facility to save our customers time, money, and hassle.
Tnemec Perma-Shield is a “fiber-reinforced modified polyamine epoxy” coating that is abrasion resistant and designed for wastewater and fume environments (“Series G436 | Perma-Shield FR”, 2021). This coating is applied to the interior of the wet well to protect the well from its contents and corrosive gases, such as Hydrogen Sulfide (H2S) gas that is commonly formed in wastewater environments. H2S is a corrosive and dangerous gas that can eat away at concrete wet wells and the mechanical within them and it is a particularly significant problem in warm environments where H2S production is increased by heat.
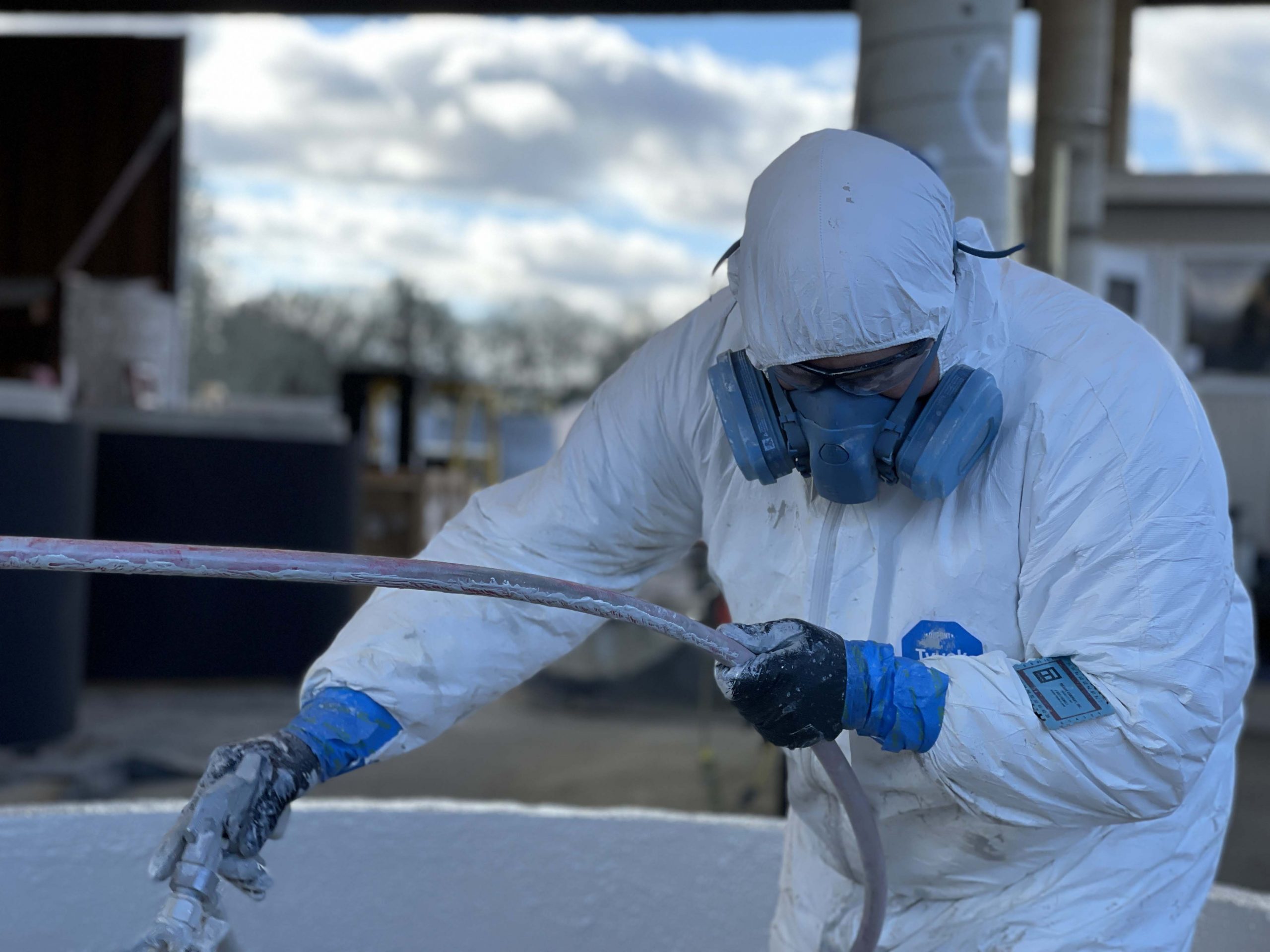
Perma-Shield is an excellent product from a well-known and high-quality brand and can be applied to the complete interior of the well prior to installation. Other coatings would need to stop before the joints and then need the joints to be coated as the wet well is being stacked at the job site. Applying the coating to the joints at the jobsite could result in improper application and curing, potentially creating problems that need repaired down the line. This is one of the benefits of Perma-Shield, Romtec Utilities can perform our quality control checks and ensure that the wet well coating has been applied and cured properly prior to delivery or installation.
The Tnemec coatings can be applied by a certified third party, but to provide the greatest benefit to our customers, Romtec Utilities has our own certified applicators that can apply the product at our facility. Applying the coatings at Romtec Utilities’ facility has numerous benefits, including the ability to control the conditions in which the Perma-Shield is applied and the ability to integrate cure times into the overall production timeline for the system.
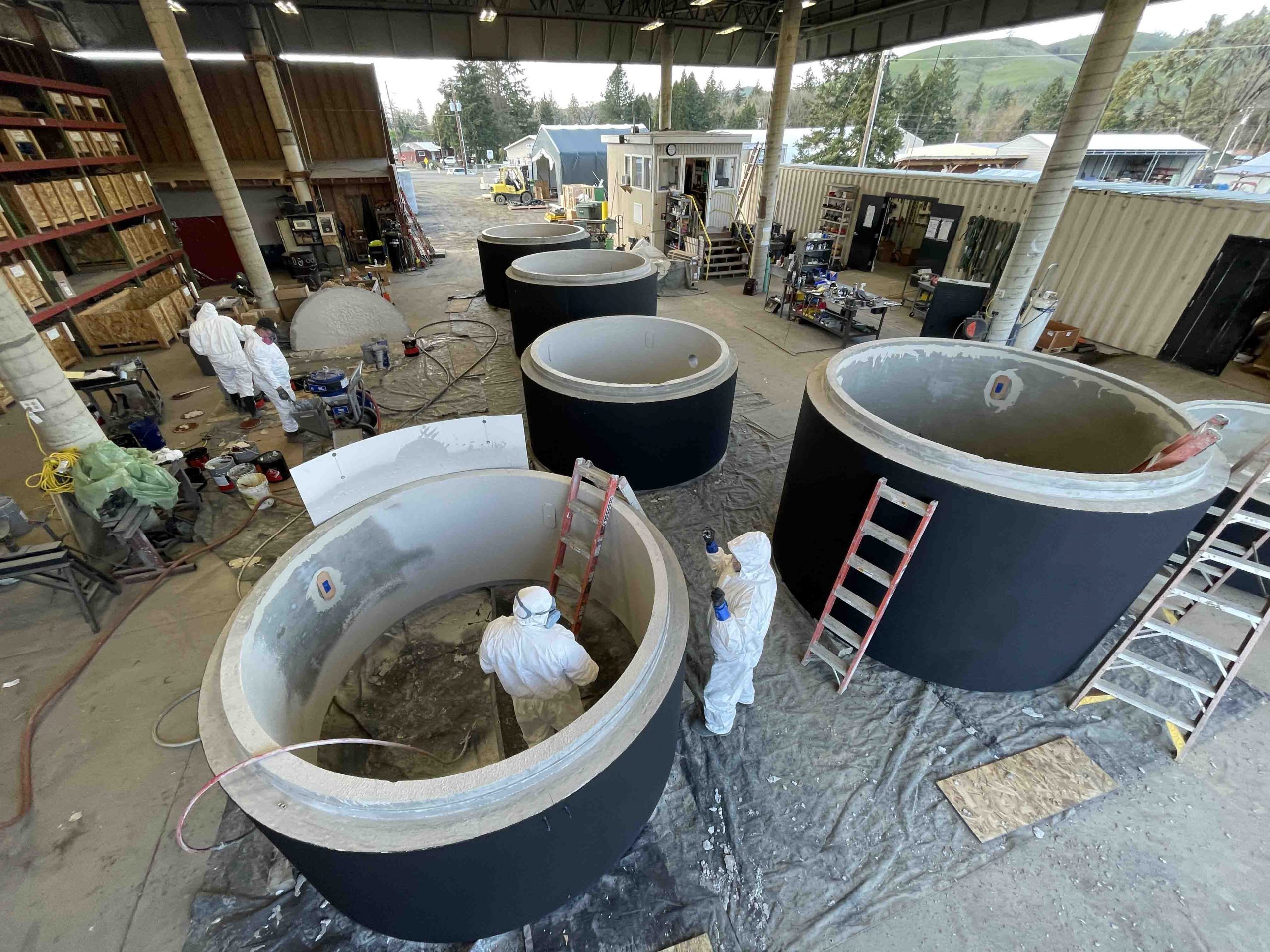
Controlled conditions are the biggest advantage Romtec Utilities can provide when applying the coating to the wet well. According to the Tnemec website, cure time on each layer of coating is dependent on the weather conditions, and at 75 degrees the coating requires 2 days to cure before being placed in service (“Series G436 | Perma-Shield FR”, 2021). Cure time increases as the temperature decreases, and the coatings need to be kept out of even common weather conditions such as rain. At our facilities, Romtec Utilities experts can provide an enclosed area for application and can control factors such as temperature that would affect the cure times. This control allows us to give our customer the best and most accurate lead times for coated wells, and easily integrate the cure times into the project timeline. Another benefit is Romtec Utilities’ “Quality Checks” that will ensure our customer gets the best product every time.
When applying the Perma-Shield coating, the preparation work is key to getting the best results possible. Romtec Utilities uses a “wet sandblaster” to sandblast the concrete and give the coating the best possible surface to adhere to. Sandblasting also exposes any small airholes in the concrete and gives Romtec the opportunity to repair holes or defects with a hardy Tnemec 218 epoxy grout. After the Tnemec 218 is applied, Romtec Utilities goes over the epoxy grout with a foam roller and water to smooth out the finish for the next step and allows the Tnemec 218 to cure for 24 hours.
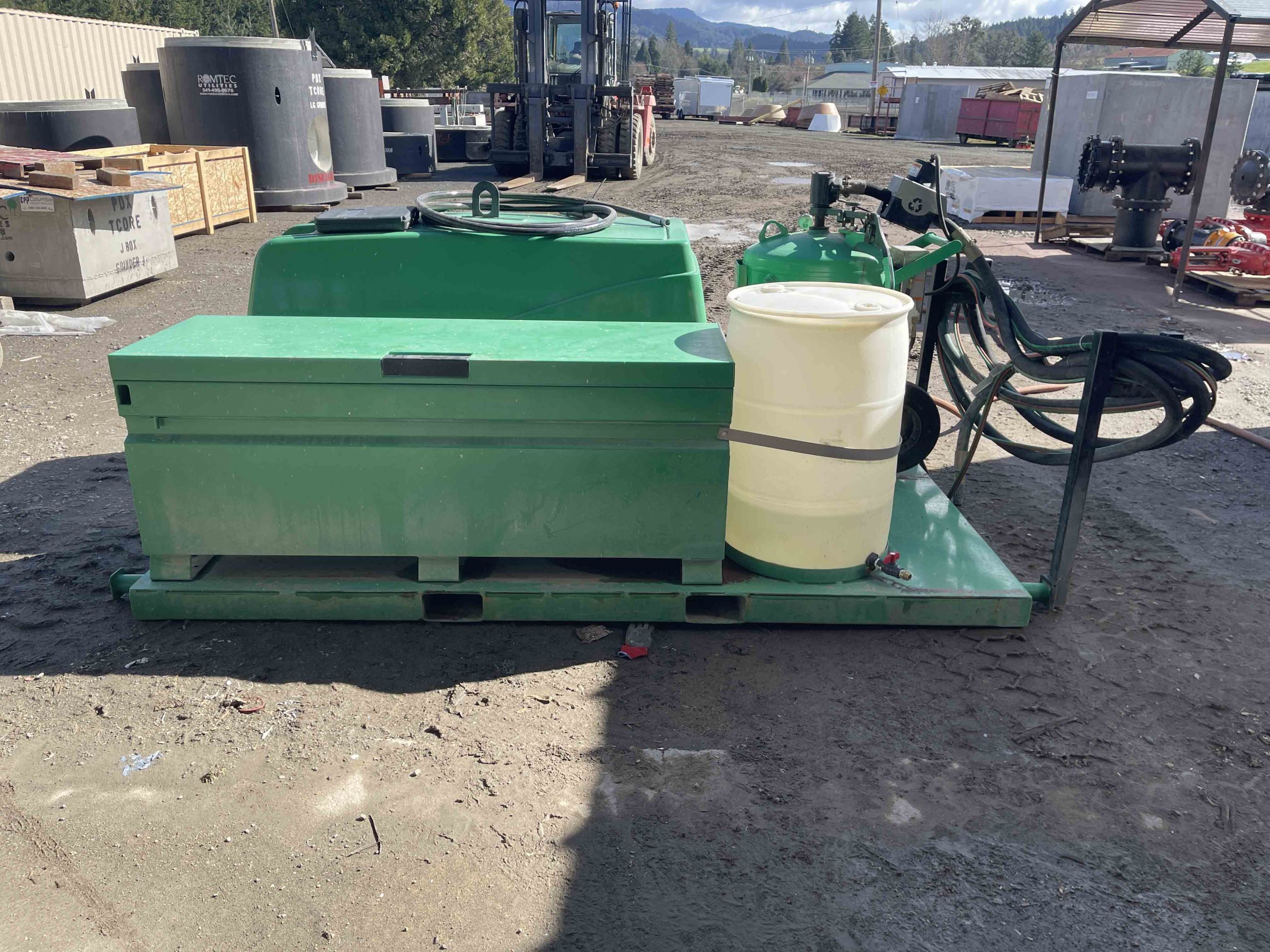
The Perma-Shield coating is a two-part mixture, Tnemec 436A and Tnemec 436B, that must be individually thoroughly mixed before being combined for a period of 3 minutes. After both parts are mixed, the coating is poured into a specialized 7000psi industrial high pressure output unit that is needed to evenly spray the thick “tar” like substance. At this point, Romtec Utilities experts must work fast to apply the coating within a 15–30-minute window. This window is entirely dependent on ambient temperature and weather conditions, making fast and efficient coating necessary.
It is important to Romtec Utilities to be able to provide what our customers want and need for their lift station systems. Wet well coatings have gained popularity in recent years, with some sewer and wastewater districts even requiring coatings on all concrete wet wells they purchase. A coated wet well can rival expensive fiberglass wet wells in their resistance to H2S gas and other corrosive materials and are more available nationwide than other well materials. To give our customers the best product possible, Romtec Utilities met with and was trained by Tnemec, and is happy to offer wet well coatings in our lift station packages for our customers.
Series G436 | Perma-Shield FR. Tnemec.com. (2021). Retrieved 23 June 2021, from https://www.tnemec.com/products/series-g436-perma-shield-fr/.