The Benefits of Polymer Concrete Wet Wells

As long as human beings have elected to hold or store liquids in ground, they have struggled with identifying the best materials for the job. The chemical make-up of the liquids and related off gassing in lift stations require different types of materials for an overall successful design. At Romtec Utilities, we are faced with these types of scenarios every day and with our professional experience, we know the right materials for the job.
In many ways the most important part of every pumping system is the material selected relative to the make-up of the liquid. That choice not only determines the life of the sump and structure, but the performance and life of all the mechanical related to the system itself.
Romtec Utilities has experience with all types of wet wells and can offer wet wells in materials such as precast concrete (with or without coatings), fiberglass, or polymer concrete. Each type has a time and a place in which it will be the best option for the system. We don’t promote any material over another because each lift station is unique in its needs, meaning there is no “one size fits all” wet well material.
Our lift stations are used nationwide across all water types, and Romtec Utilities incorporates the best equipment and materials to meet the standards or requirements of the end owner and reviewing entities. Romtec Utilities knows that customers and reviewing agencies have their own standards that vary from district to district, and may require a specific material for the wet well.
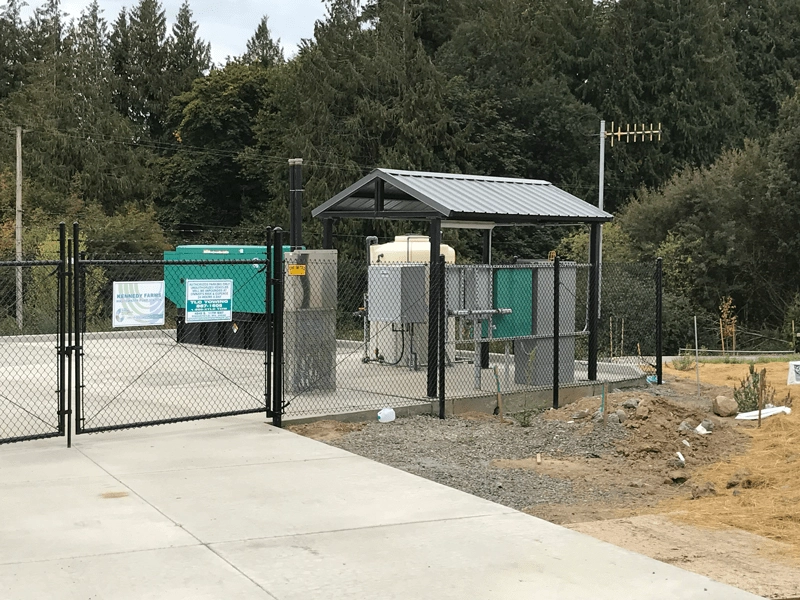
Understanding the different wet well materials is important. Not only does it help Romtec Utilities determine the best equipment for the lift station, but it also helps us to better meet the standards of our customers. Precast concrete (with or without interior coatings), fiberglass, and polymer concrete wet wells have all been incorporated into Romtec Utilities’ lift stations and have their own distinct advantages and disadvantages.
Precast concrete is the traditional option for wet wells and is frequently supplied on our projects. These wet wells have the benefit of lower cost and easy availability nationwide, as well as easy workability relative to Romtec Utilities’ high-level prefabrication. Precast concrete, however, is susceptible to Hydrogen Sulfide (H2S) corrosion or corrosion from acidic waste. To combat this issue, Romtec Utilities has familiarized ourselves with well coatings and their application.
Coatings on the interior of the wet well prevent the H2S from coming into contact with the concrete. Some sewer districts, such as the Clark Regional Wastewater District (CRWWD) in Washington, even require that precast wet wells have exterior coatings. Interior coatings will help to deter the corrosion and can extend the life of the well, however, they also require extra time and money on a project with additional preparation, application, and cure times for each layer.
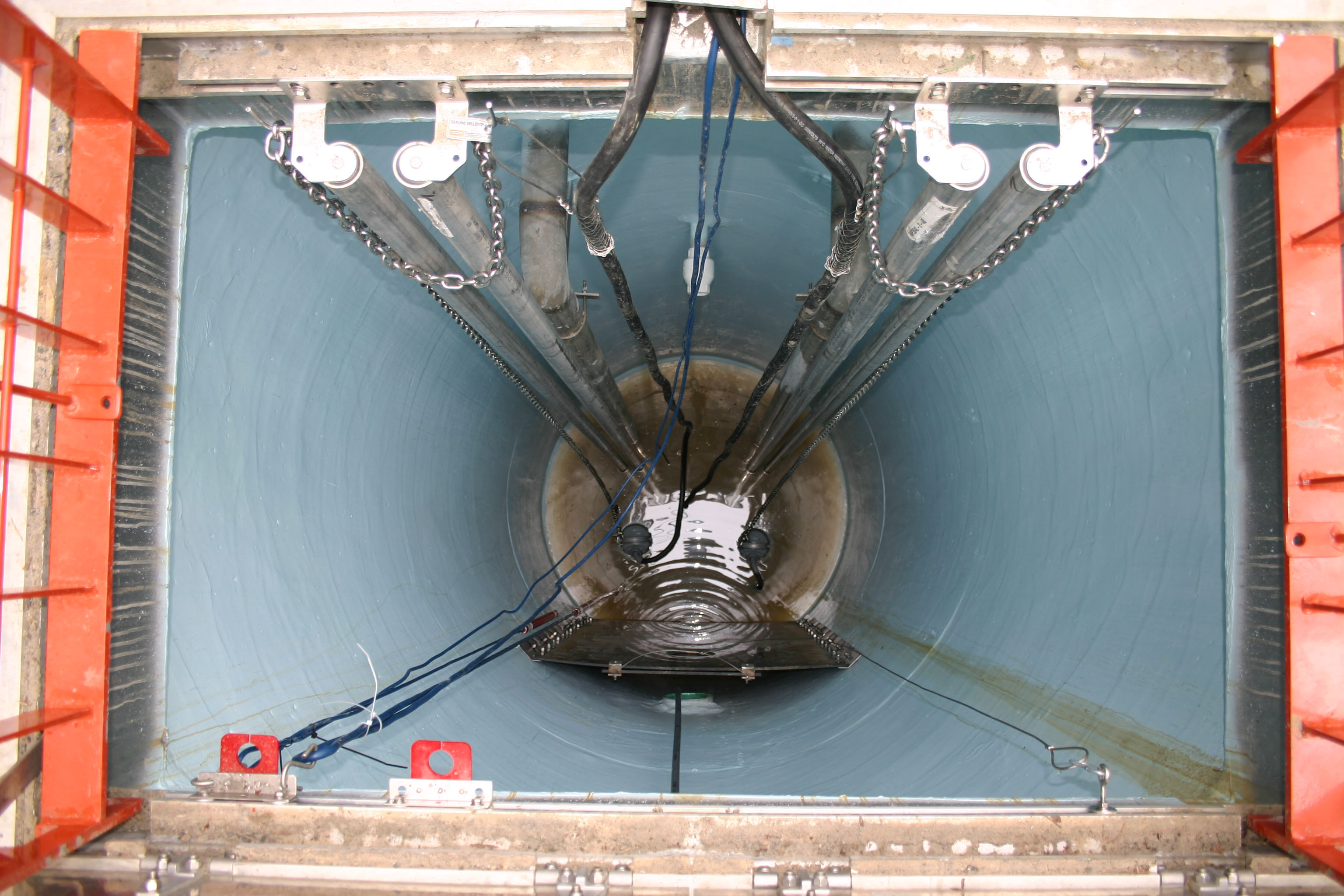
Precast concrete is a widely available material that is easy to work with, but even with coatings they are susceptible to cracking from ground water pressure and age.
Fiberglass is more resistant to structural degradation than concrete when it comes to pressure and corrosion. Fiberglass wet wells also tend to age better than concrete wet wells, and can greatly reduce the maintenance and replacement costs down the line. While it can extend the life of a wet well, fiberglass comes with a high cost, and some disadvantages.
Aside from the price tag, one of the biggest disadvantages is that fiberglass is not as easy to work with as concrete. Once the mold for the wet well is finished, changes throughout production can be time consuming, costly, and even create problems later on. The quality of the fiberglass can also be very dependent on the manufacturer and vary across the United States.
For a long time, the primary wet well options for harsh environments came down to high quality precast concrete with coatings or high-quality fiberglass. The innovation of polymer concrete takes many of the advantages of high quality precast with coatings and combines them with advantages found in high quality fiberglass, all the while maintaining workability.
The cost of polymer concrete is more expensive than traditional concrete, but can rival the cost of concrete wet wells with coatings. Polymer concrete wet wells are already resistant to corrosion, which eliminates the time that would be needed to prepare, apply, and cure the coating layers.
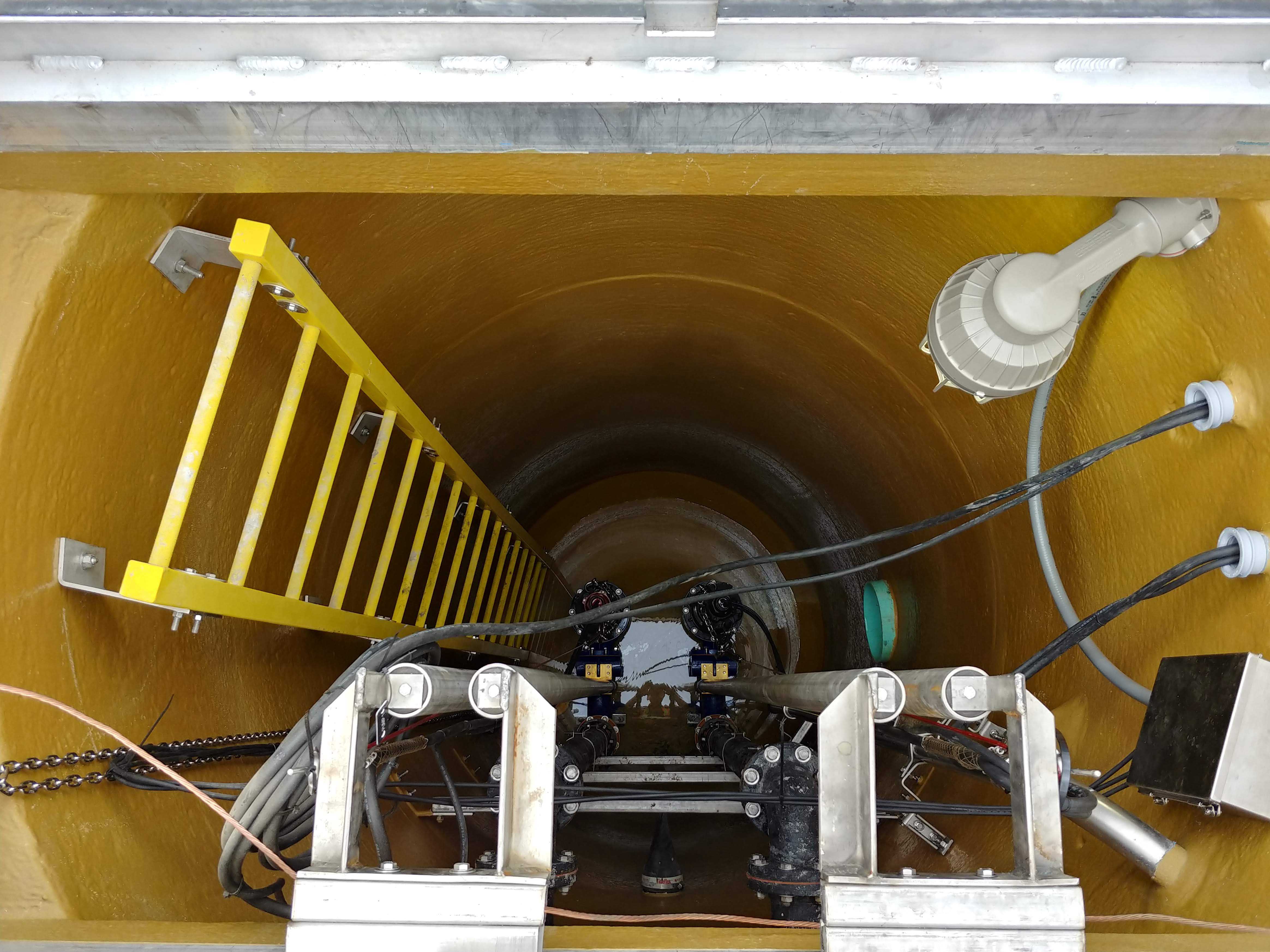
In addition to the corrosion resistance, polymer concrete wet well wells are also stronger than concrete wells. While traditional concrete wet wells are subject to cracking from outside pressure, polymer concrete is “8 times stronger in flexural and 4 times stronger in compression than traditional concrete”, according to the Armorock website. Armorock is based in Nevada, and is a supplier of polymer concrete wet wells that Romtec Utilities has worked with on multiple projects. Their polymer concrete “exceeds 16,000 PSI in compression and flexural breaks exceeding 2,000 PSI”.
However, despite the many benefits and advantages to polymer concrete, there are some disadvantages to this material. Polymer concrete is more expensive than traditional precast concrete, and the biggest disadvantage for polymer concrete wet wells is that they are not as readily available across the United States as concrete or fiberglass.
While polymer concrete wet wells are more expensive and less available than the traditional options, they are well suited for corrosive environments, and can make a world of difference in hotter environments that experience increased H2S gas formation. Polymer concrete helps to bridge the gap between high quality precast with coatings and high-quality fiberglass.
Romtec Utilities experts have designed lift stations with wet wells from all of the material types above, and apply their knowledge to determine what material would be best not only for the life of the lift station, but also our customers’ needs. Whether it is polymer concrete wet wells, fiberglass, or concrete (with or without coatings), Romtec Utilities can supply the best wet well for each unique situation.