A prefabricated fiberglass, steel, or stainless steel wet well structure requires more work when designing and constructing it within a pump station. Although some projects may require a fiberglass, steel, or stainless-steel sump, these materials can be hard to work with.
Therefore, there should be special consideration when using these types of materials to create a wet well structure.
When working with any of these three materials there are 3rd party manufacturers involved and they are not as forgiving. Any error or defect in the sump structure requires the manufacturer, and/or specialty tools/personnel to repair. This can be a big headache, so having a backup plan in place is always a good idea if a defect occurs.
The repair material is not as readily available as that of concrete or grout. This can make the repair take longer to finish, which may cause delays in the operation of the system which can be a bigger headache to handle. That is why having a contingency plan in place is important when using a prefabricated sump made of fiberglass, steel, or stainless steel.
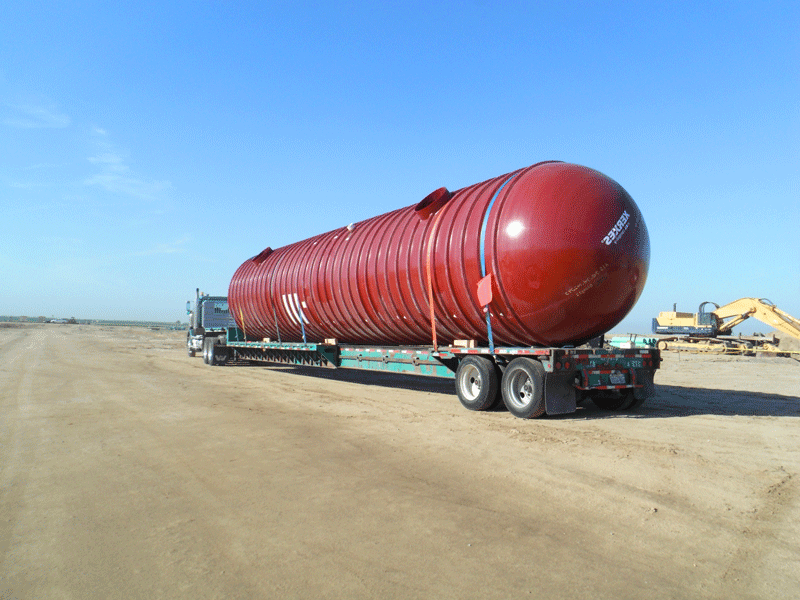
What is Being Pumped
Steel, especially stainless steel, is resistant to high water temperatures and many types of corrosive or caustic conditions. Like concrete, steel has tremendous availability in terms of manufacturers and experience. The major drawback to using steel or stainless steel is that it can be very expensive. This material is also very responsive to market conditions, creating costs that can fluctuate drastically in short periods of time.
Fiberglass is a great material for structures where corrosive or other volatile fluids need to be pumped. Using fiberglass will eliminate the need for a coating or liner on the structural components.
Fiberglass can also be fabricated in a double-wall method which offers structural redundancy and the capability for leak detection systems. Fiberglass is not as widely available, and there can be restrictions on the full size and shape of the structure.
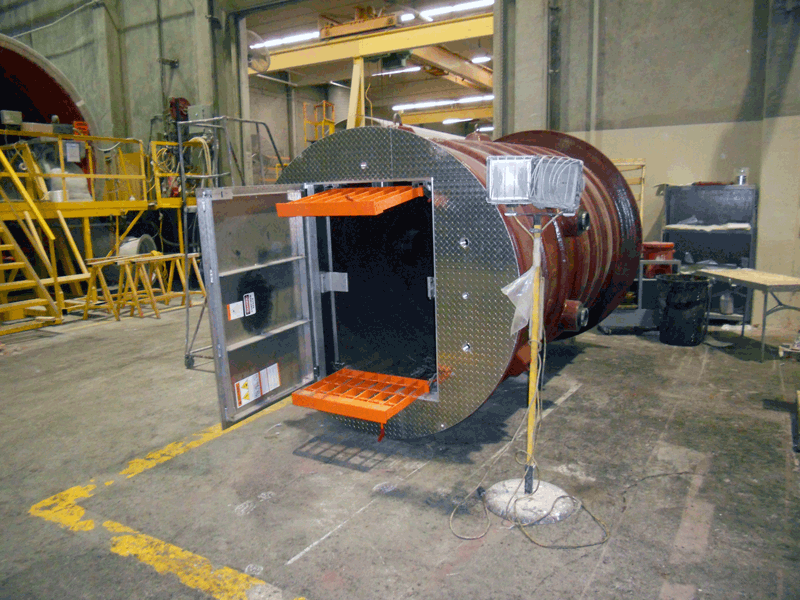
Staging, Logistics, and Installation
These materials are typically cast as a complete structure. This means that storage and shipping must be taken into consideration ahead of time.
The facility to perform the prefabricated work must be large enough to accommodate the structure.
These materials often require specific installation requirements such as unique drainage plans/materials, as well as handling instructions during the process.
All these details are taken into consideration at Romtec, as we design and supply the entire pump system including the wet well working with 3rd party vendors and suppliers.
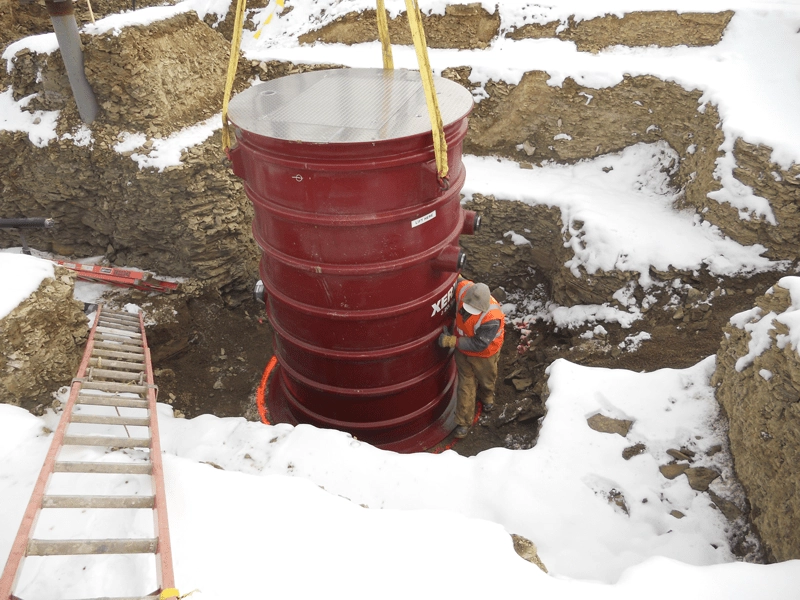
More Prefabrication
Since the sump is a single piece, more (if not all) of the internal components will be installed prior to shipment. This allows for ease of installation for the on-site contractor.
More prefabrication in a controlled environment reduces the chance for error in the field. If the internal components were installed in the field, then the structure could be damaged. This would be harder to repair in the field than in a controlled environment.
These materials will require more work to be done than a precast or polymer wet well/ sump.
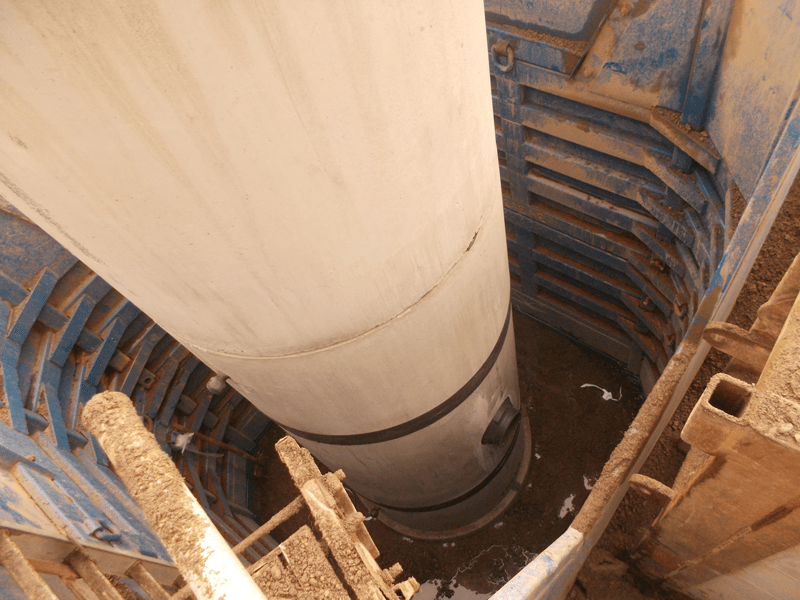
Precast or Polymer Wet Wells
Concrete can be cast in place, but precasting structural materials offers a higher degree of quality control and component prefabrication.
This is a great material in terms of cost, durability, availability, and lead times. The only drawbacks to this material are its size and weight, which can increase demands during shipping and installation. All concrete can also be susceptible to corrosion that can weaken the material. But the market offers a wide variety of coatings and liners, to mitigate the damage corrosion can cause with concrete.
Polymer concrete is another material that is seeing more common use. It is not technically concrete but rather a polymer resin that is cast in a similar process to concrete. It can be cast in thinner pieces than traditional concrete, creating structural components that weigh less than comparable concrete components.
Additionally, polymer concrete offers many advantages over fiberglass. As a synthetic material, polymer concrete can be fabricated to resist many types of corrosive and caustic water types. As a growing structural material, polymer concrete is currently not as readily available and cannot always be fabricated in every shape and size.
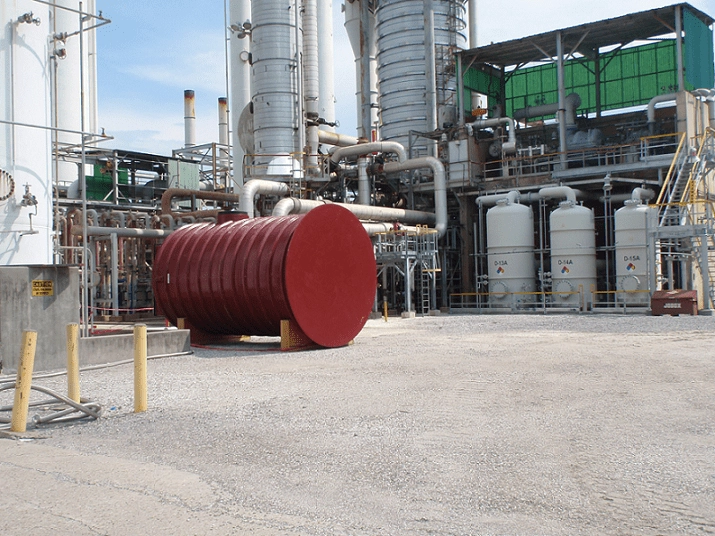
Fiberglass, Steel, and Stainless Steel = More Requirements
Some things to remember when using a fiberglass or steel wet well includes the 3rd party manufacturers and remembering that the materials are not as forgiving or easy to repair as concrete or grout. Logistics and installation must be considered when working with these prefabricated sump structures that are large and have special considerations.
There is also more prefabrication done on the internal components of the wet well which allows for easier installation by the on-site contractor.
Overall, it takes more work to create a fiberglass, steel, or stainless-steel sump but if it’s necessary for the water type or application, then it’s worth the extra time.
The structural materials used for vaults and wet wells are always applied with the specific design requirements of each pumping system.
Included in these requirements are the preferences and standards of the customer or system owner.
Romtec Utilities works with each customer, their engineers, and the specific pumping requirements to propose the best structural materials in terms of life span, durability, cost, lead time, and ease of installation.
For corrosive or volatile fluids, fiberglass wet wells are a great option. It can be built with a double wall for redundancy and leak detection.
While steel is resistant to high water temperatures and many types of corrosive or caustic conditions.
Both prefabricated steel and fiberglass sumps are a great solution for certain pumping environments, depending on what is being pumped and the owners’ preferences on the design, expense, and installation of the system.
At Romtec Utilities we design and supply the complete system to cater to the project needs, pumping environment, and owners’ preferences on every aspect of the entire system. To create a pumping system for your project, contact us today to get started on the design process.